Así es por dentro la fábrica de un equipo de Fórmula 1, un búnker donde nadie puede grabar
Relevo visita la sede de Alpine F1, el cuarto mejor equipo de 2022, para descubrir algunos de sus secretos.

En sus pasillos no existen olores, apenas ligeros aromas a materiales de última generación. Las conversaciones se desarrollan en voz baja y las miradas de reojo a los visitantes externos generan cierta tensión momentánea. En las pocas pantallas de ordenador a las que se puede llegar a echar una mirada furtiva, aparecen diseños 3D de diferentes piezas, con colores fosforescentes y cientos de números asociados a ellas. Al doblar una esquina, uno se encuentra con un grupo de cinco mecánicos que se afana por completar el ensamblaje de una de las dos unidades del Alpine A523 que competirá en la Fórmula 1 2023. Estamos en Enstone una fortaleza tecnológica donde cada segundo de trabajo vale varias centenas de miles de euros.
Ubicadas a unos 120 kilómetros del Big Ben y la Abadía de Westminster, las instalaciones del equipo Alpine F1 se alzan en el espacio que hasta 1991 ocupó una antigua cantera, antes de que el equipo Benetton construyese allí su sede. Donde hace tres décadas se extraían materiales para la construcción a cielo abierto, hoy se construye bajo techo el futuro de un proyecto que sueña con volver a inscribir su nombre (desde 2021 con la denominación de la marca deportiva del grupo Renault) en los trofeos de plata de campeones del mundo. Unas mieles que sólo lograron saborear en 2005 y 2006 de la mano de Fernando Alonso ya con Renault a los mandos, y anteriormente, en 1994 y 1995, con Michael Schumacher, bajo el nombre de Benetton F1 Racing Team.
El camino hasta este lugar recóndito discurre entre prados verdes, cancelas de madera, edificios de piedra vista y chimeneas humeantes durante un día gris y lluvioso de mediados de febrero. Las ovejas sin esquilar pacen a sus anchas entre algunos árboles dispersos y arremolinadas entre sí para protegerse de las bajas temperaturas. Pocos dirían que en unos 100 kilómetros a la redonda se encuentran ubicadas cinco de las diez escuderías de la Fórmula 1, uno de los deportes más tecnológicos del planeta. No existen señales que te lleven hasta la sede de Alpine F1. Apenas un pequeño cartel con el nombre de la marca francesa sobre fondo blanco figura a un lateral de la garita del control de acceso, rodeado de setos sin hojas, con ramas desnudas que se entrecruzan disimuladamente, como si no quisieran llamar la atención de cualquier despistado que llegue a estas coordenadas.

En el aparcamiento, donde los895 empleados del equipo dejan sus coches cada fría mañana, no se ve ningún Alpine A110, la joya de la corona de la división deportiva de Renault. Las salas donde se ubica el Centro de Investigación de Aerodinámica Computacional son una especie de búnker cubierto por una pequeña colina, donde solo entra la luz solar a través de cuatro grandes claraboyas. Antes de poner un solo pie en su interior, los pequeños objetivos de los teléfonos móviles deben ser precintados con unas tupidas pegatinas rojas donde se recuerda al visitante que está terminante prohibido grabar o fotografiar nada que encuentre a su paso desde ese momento. Para evitar cualquier tipo de tentación, la cámara frontal, camuflada dentro de la pantalla, también recibe otra lámina roja con pegamento.
Un muro de boxes en la fábrica
Una vez se traspasan las puertas del edificio principal, el A521 de 2021, con el que Esteban Ocon logró su primera victoria en el GP de Hungría y Fernando Alonso su último podio, por ahora, en el GP de Catar, recibe al visitante flanqueado por una vitrina de trofeos y una réplica de exhibición del Renault R25. La primera parada es una amplía sala acristalada con unos siete monitores de 75 pulgadas en la pared de enfrente a la entrada y 24 asientos, con sus respectivas pantallas dobles de 24 pulgadas cada una. Esta es la llamada Sala de Estrategia Remota, donde se recibe en directo toda la información desde cada Gran Premio, sea donde sea. La conexión es directa con el muro de boxes y desde aquí se pueden escuchar todas las conversaciones con los pilotos, el jefe de mecánicos o el jefe de rendimiento. Además, también se permanece en contacto con Francia, donde se encuentra la fábrica de motores de Renault, en Viry-Chatillon, a 30 km de París.
Después de cada sesión, los ingenieros presentes en la sala hacen un escaneo completo de la telemetría de cada componente del coche para revisar que no haya habido fallos. También se ejecutan miles de simulaciones para valorar las estrategias de la carrera del domingo. El objetivo es que, a primera hora del día siguiente, los ingenieros que están en el circuito tengan toda la información posible a su disposición. Para ello, hay más de 200 sensores en cada monoplaza que ofrecen 150.000 mediciones por segundo (temperaturas, presiones, aceleraciones, etc), el equivalente a 4 MB de datos por segundo. Todo esto llega desde cualquier circuito del mundo a esta sala de Enstone en cuestión de apenas… ¡0,25 segundos! A lo largo de la temporada se recogen 102 millones de estadísticas y se realizan 1.500 millones de simulaciones de estrategia, con el objetivo de obtener los mejores resultados en pista posibles.
El lugar donde nacen los F1
Nada más salir de la Sala de Estrategia Remota, una pequeña barandilla de aluminio a la altura de la cintura hace las veces de mirador del espacio donde se ensamblan los monoplazas. Abajo, en los dos espacios separados por encimeras blancas e impolutas, llenas de cajones con tornillos, engranajes y herramientas, aguarda bajo una lona negra uno de los dos chasis que Alpine F1 logró terminar antes de los test de pretemporada. Este fue transportado dos días después de la visita en un Boeing 777 dentro de un contenedor con forma de prisma hexagonal hasta Baréin.
Pero para que esto ocurra, se han tenido que emplear 400.000 horas de trabajo y 16.000 diseños digitales para definir los 13.000 componentes de un coche, algo que comienza 18 meses antes de la nueva temporada para tener el primer chasis listo antes de las Navidades.
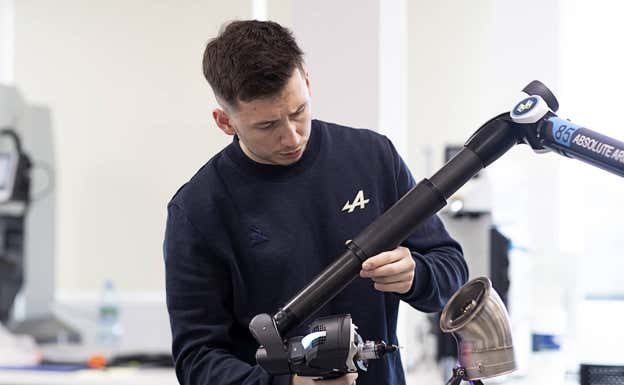
Es aquí adonde regresan los monoplazas, previamente desmontados (en unas cuatro horas) y con sólo la suspensión delantera instalada, como mucho, tras un fin de semana de carreras. En el caso de las citas europeas, los coches llegan el lunes o martes y el jueves por la tarde ya se han revisado pieza por pieza y están preparados para el siguiente Gran Premio gracias al trabajo de diez mecánicos.
En la planta de abajo es donde se encuentra la sección de Fabricación. En ella trabajan alrededor de 200 personas, 60 de ellas en el taller metálico y otras 150 en la parte de Composite. Alpine F1 tiene la capacidad de construir el 90% de los componentes de su chasis y el 85% del total del coche. Este es el corazón de Enstone, que está en marcha 24 horas cada día y los siete días de la semana. Al fondo, entre un sinfín de tubos, conexiones y estanterías, es donde se fabrican a mano (sí, has leído bien) los sistemas de refrigeración, los escapes y otras piezas mecánicas pequeñas. "Es un oficio en extinción, peromuy valioso aquí en Alpine. Por ejemplo, los escapes se construyen con finas láminas de Inconel (aleación con alto contenido en níquel que aguanta altas temperaturas). Son piezas que van de los 1,1 milímetros hasta los 0,3 en la parte más externa", cuenta el responsable del departamento.
Otra de las joyas de la corona es la sala de Composite, donde se fabrican todas las piezas de fibra de carbono (un material cinco veces más ligero y el doble de resistente que el acero) de los Fórmula 1. En esta entran los moldes de las mismas, que se terminan a mano. Pero esta instalación cuenta con una particularidad: en su interior hay presión positiva y la limpieza debe ser extrema, al estilo de las empresas aeronáuticas. El motivo: cualquier mota de polvo puede meterse entre una lámina de carbono y otra y afectar al aspecto final, su resistencia y su longevidad. Por eso, todos los trabajadores visten un mono azul oscuro que se ponen por primera vez antes de entrar a la sala completamente acristalada; sus zapatos deben pasar por unas alfombrillas pegajosas que eliminan la suciedad. En el techo están instalados unos sistemas láser azules que se proyectan en los bancos de trabajo para indicar la orientación de cada pieza y por dónde hay que cortarlas con una precisión total. "Antes era un hombre con unas tijeras el que cortaba, ahora todo se hace con láser, para eliminar cualquier pequeño error", añade el responsable.

Por temporada, se utiliza el equivalente a una lámina de carbono de 18 km de largo por un metro de ancho, nada menos. Así mismo, en esta planta se ensamblan 100.000 piezas de metal al año gracias a las nuevas máquinas que se instalaron en 2018, que han mejorado su precisión en un 30%. Además, Alpine cuenta con un departamento de Electrónica de 28 personas, responsables del volante, las comunicaciones por radio, el sistema de control de las paradas en boxes y de los sistemas de telemetría. En esta sede también se construyen las cajas de cambios, de 9 velocidades, en fibra de carbono.
El simulador, una réplica virtual de la realidad
Para llegar al edificio donde se encuentra el simulador hay que salir a un pasillo al aire libre entre la nave principal y otra secundaria que está en obras (donde se ubican las máquinas CNC, que construyen componentes con alta precisión). El aspecto exterior recordaría al de cualquier polígono industrial de la periferia de Madrid o Barcelona. En una tercera nave está el centro de pintura, donde se vinilan y se pintan las piezas externas de cada monoplaza. En el momento de la visita, por ejemplo, estaban trabajando con dos de los nuevos pontones del A523, rosas, azules y negros carbono.
En la puerta de al lado está la sala del simulador (creado en 2011), que lejos de ser la gigantesca 'araña' que tenía Ferrari en Maranello, en el caso de Alpine son dos pequeñas estancias. La primera, con varias pantallas a la altura de los ojos y al borde del techo donde se ven en directo cientos de datos de telemetría con diferentes líneas de colores (verde, rojo, morado, azul, amarillo…) que indican distintos valores del vehículo como aceleración, velocidad, frenada, etc. Aquí trabajan varios ingenieros a las órdenes de Ben Morgan. Al otro lado de una mampara de cristal está la recreación del chasis, a escala real, sobre una plataforma de movimiento que recrea las fuerzas que recibe el monoplaza. Enfrente: una pantalla de cine de alta definición que ofrece una visión de unos 180º al piloto.

Cada piloto titular pasa por aquí "unos 15-20 días por temporada", según Morgan, como fue el caso de Fernando Alonso, que tuvo que trabajar durante horas para encontrar la solución a los problemas de dirección asistida que tuvo durante los primeros seis meses de la temporada pasada. El modelado del monoplaza es obra 100% de los ingenieros de Enstone, pero los mapas de los circuitos, escaneados por láser y actualizados cada temporada, los suministra la empresa rFactor Pro. Tres cuartas partes de la energía utilizada por esta instalación procede de los paneles solares que tiene la fábrica (33.000 kWh al año, unas 10 veces más de lo que consumimos en nuestras casas).
Todo esto permite realizar simulaciones de cualquier aspecto que el piloto o el equipo necesite y son extrapolables a la vida real. De hecho, el simulador puede rodar por sí mismo sin un piloto en la cabina para recabar datos cuando sea necesario. Es aquí donde también se van probando conceptos para el futuro, como las suspensiones de 2024 o algunas simulaciones de cara al gran cambio de la normativa de motores para 2026. En lugar de viajar hasta un circuito y realizar un test real (algo prohibido por el reglamento de la FIA desde hace años), los equipos de F1 tienen así más flexibilidad y se ahorran millones de euros con este tipo de instalación.
El búnker de Alpine F1
Unos cuantos metros bajo tierra se encuentra el túnel de viento, lugar absolutamente clave a la hora de diseñar un F1 actual e inexpugnable. El de Enstone se construyó en 1998 y ocupa 2.674 metros cuadrados. Actualmente, la normativa de la FIA permite un uso controlado en función de la posición en la general de Constructores de cada equipo la temporada anterior. Esta instalación permite que un coche (a escala 60%, en este caso) se coloque en un tapiz rodante con una corriente de aire fluyendo a su alrededor para que los ingenieros comprueben los resultados de sus diseños aerodinámicos. Ocho meses antes de la primera carrera, es aquí donde se empiezan a probar las novedades antes de viajar a los test de pretemporada.

Este departamento se complementa con el de CFD (Dinámica Computacional de Fluidos, por sus siglas en inglés), que ha revolucionado desde hace años el diseño de los F1. Este permite a los ingenieros, a través de un software de última generación, simular cada milímetro del coche y cómo influye el aire en él. Para ello, producen cada semana 60 TB de datos que les ayudan a plasmar sus hallazgos en el monoplaza.
Todo el trabajo que se cuece a fuego lento y rápido, en función de las necesidades, en los terrenos de la antigua mina se traslada a la pista con un equipo de unas 100 personas, de las cuales 60 de ellas trabajan directamente en el coche. En este rincón de la campiña de Oxfordshire es donde dos de los grandes nombres de la leyenda de la F1 marcaron su destino, dos pilotos franceses, Ocon y Gasly, buscan ahora seguir sus pasos.